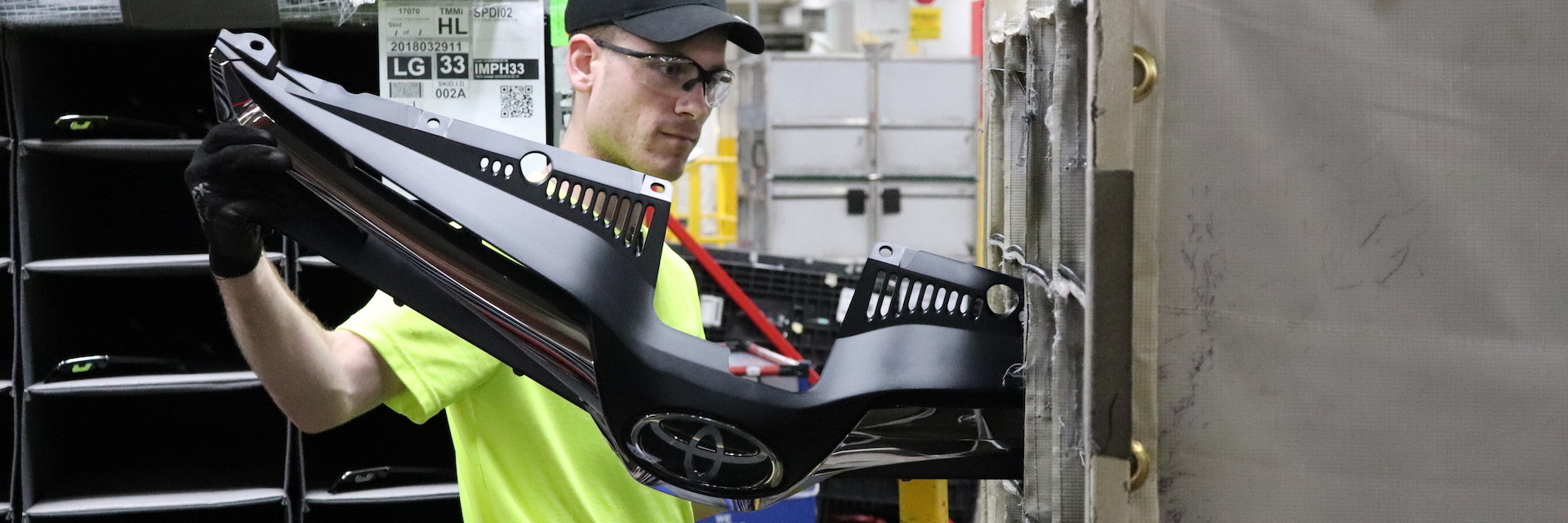
Toyota’s Indiana Plant Creates Job Pathways for People Living With Disabilities
Ted Brown has accomplished a lot over his 24-year career at Toyota Motor Manufacturing, Indiana (TMMI). But as far as he’s concerned, none of it measures up to the achievements of people like Dakota Moore.
“He’s got a cool story,” says the vice president of Administration at the Princeton, Indiana, facility. “Dakota is a Special Olympics athlete. He’s competed on the national stage and has won silver and bronze medals. And just this past summer, he won five gold medals in weightlifting/power lifting. And Dakota bought a new Corolla. His parents didn’t do that for him. He did it. On his own.”
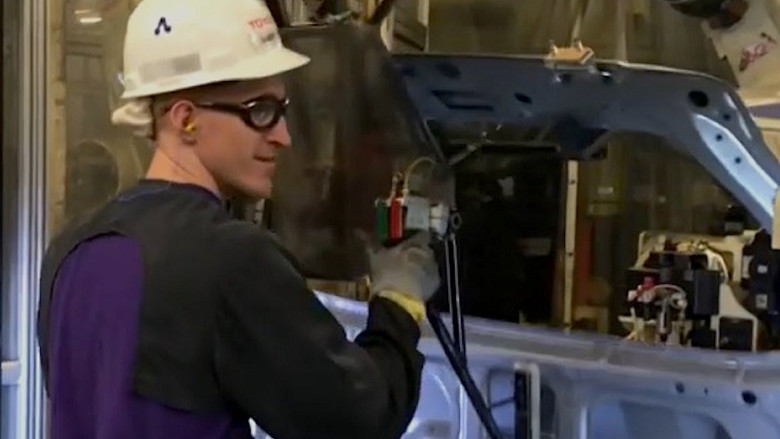
On a Roll — Thanks in part to the confidence gained in working at TMMI, Dakota Moore has competed on the national stage in the Special Olympics, recently bought a Corolla, got engaged and with his fiancé bought a house.
In 2021, there were about 30 people with disabilities working on the TMMI campus. And today, that number has risen to nearly 100. Moore has been part of that growth, as a mentor for new team members. These remarkable individuals have overcome physical, mental and emotional challenges to make the journey from complete dependence on others to a high level of independence as full-time team members at TMMI.
Suppliers at TMMI have also followed suite to participate in hiring people with disabilities.
For Brown, it’s a dynamic that hits close to home. Twenty-six years ago, his son Zach was born with spina bifida. His hope? By helping others gain a measure of control over their lives, perhaps he and his wife Michelle can do the same for their son, too.
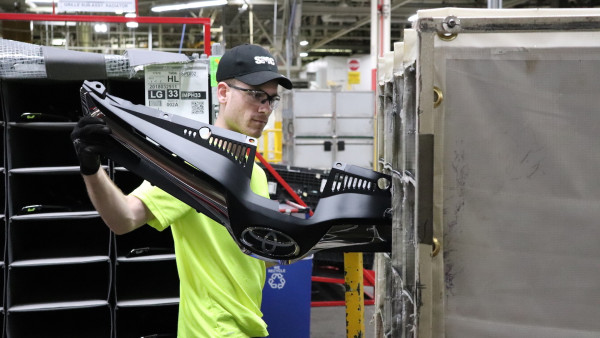
Pride and Joy — Zach Brown, son of TMMI's Ted Brown, was born with spina bifida. But that hasn't prevented the 26-year-old from finding a place of productivity at the plant.
Success Nine Years in the Making
So, in 2014, Brown and other like-minded colleagues established an enclave — or workspace set apart from the mainstream flow of other employees — within TMMI’s East Plant. There, workers living with disabilities were given such tasks as assembling jack packages and window switches for the Sienna. The success of that model led to the creation of a second enclave in the West Plant about a year later.
Then in 2017, TMMI formed a partnership with ARC of Gibson County, a public agency that has been helping people living with disabilities since 1963. Its New Frontiers training focuses on such fundamentals as interviewing and job seeking skills, resume writing and onsite job coaching. Through this alliance, the plant was able to create a framework within which some of the workers could develop the skills and experience needed to transition from their enclave to full-time employment and fuller autonomy on the facility’s sprawling campus.
TMMI transformed its East Plant enclave into an in-house training center to provide additional support to workers who aspire to achieve more. Brandon Wilson is among the many who’ve benefitted from that change.
“He had been working in the training center for about six months and had seen some of his friends make the transition,” says Brown. “So he took it upon himself to apply for a job. He didn’t tell anyone. And he got it. It’s so great to see that initiative.”

Mr. Reliable — John Hardiman hasn't missed a day of work at TMMI in over seven years.
Another beneficiary has been Corey Wilkerson. After getting his start in an enclave, he found his niche on one of the plant’s janitorial teams. In 2021, he was promoted to team leader and has since advanced to another one of Toyota's suppliers.
And then there’s John Hardiman, who’s also made the transition from the training center.
“He’s never missed a day in over seven years,” says Brown. “He picks seatbelts. That might sound like trivial work. But part accuracy is an important step in the production process. Delivering the right parts to the line, at the right time and in the right sequence, helps to maximize production efficiency. Everyone here does important work.”
Brown loves to share these stories. Not only is he proud of people like his son who’ve risen above their challenges to succeed, he’s also grateful for the contributions they make to TMMI every day. Absenteeism among this group is extremely low. Productivity is very high. And the passion they bring to their work is infectious, inspiring everyone who comes into contact with them to dig deep and do more.
“Between TMMI and our suppliers, there are 10,000 jobs within a 2.5-mile radius of where I sit,” says Brown. “Every single one of them is important to our objective of assembling high quality vehicles. You need the right parts to show up at the right time and these people are delivering on that. If they work in a cafeteria, it’s important that they get the food out on time. They are doing that. Same for the janitorial service. Everyone who works with these folks raves about their work ethic.”

Happy Camper — Katlin Slough started in an enclave, worked in the training center and is now a full-time employee of one of TMMI's on-site suppliers. "She has been very successful," says Brown. "Smiling every day with a great attitude to keep improving herself."
The Power of TMMI’s Example
TMMI has made a lot of progress on this front over the years. But it’s not Toyota’s only North American plant that recognizes the benefits of creating work opportunities for people with disabilities. For instance:
- Toyota Motor Manufacturing, Kentucky established its first enclave in 2010.
- Toyota Motor Manufacturing, West Virginia followed suit in 2018 and, since then, enclave workers have built components for over 1 million 4- and 6-cylinder engines. According to Mike Bush, manager of Talent Management, enclave workers continue to take on more complex tasks, having successfully completed training to build components for the new TNGA-2 2.4L Turbo Engine Line. Looking to Phase 2, integrated technologies at the enclave will allow for continued diversification of products and increased responsibilities for the workers.
- Toyota Motor Manufacturing, Texas is well underway with construction of its ToyotAbility Workforce Center. “As we are doing everything possible to eliminate unnecessary costs, we’re also investing in our team members with a home base to support and grow successful manufacturing team members,” said Rob Franklin Group Manager, Transformative Manufacturing, TMMTX.
Meanwhile, Brown is committed to creating additional pathways for people with disabilities at TMMI. He led the launch of TMMI’s apprenticeship program in 2020. To date, they’ve had 26 apprentices, gave job offers to 25 with 24 accepting. And after two years, 16 continue to work at TMMI. Class size has grown three-fold from 2020, now with six workers per session.
We know one size does not fit all, so we’re trying to create a broad spectrum of opportunities, Working with people living with disabilities makes Toyota a stronger company. This is what Respect for People is really all about.